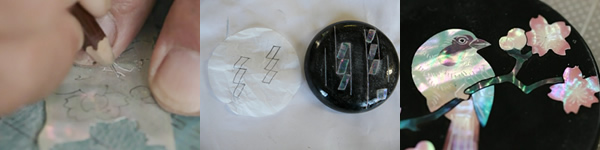
Design and colour worked out by professional craftsman.
Craftsman’s heightened sensitivity and sophisticated skills.
Subtle glitter created by craftsmanship developed and improved over the years.
Rich lacquer and shining of “Raden” create the world of beauty.
This is the fruit of beauty produced by sensitive technique of Japanese professionals.
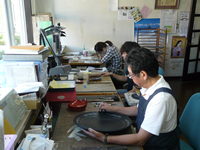
Takaoka lacquerware has over 400-year history. It was started in Edo Era, and various techniques such as Sabie, Raden and so on were created afterwards.
Out of these techniques, “Aogai-nuri” has 11 processes until its completion and this Master’s technique has been enabled only by skilled craftsman.
*Takaoka lacquerware was recognised as national traditional crafts in September 1975.
Traditional craft: all hand-made with history of over 100 years; to be produced by special technique;
selected products designated by Ministry of Economy, Trade and Industry.
“Aogai-nuri”: Technique to portray landscape/birds and flowers, with a combination of triangle or lozenge shaped thin pieces of shells made by knife or needle. Shells used for these decorations are abalone, pearl-shell, silver-lipped pearl oyster (white-, black- brown- mother of pearl), box mussel and so on. These pearl-coloured shells match well with lacquer and create unique appearance.
Process to make “Aogai” – “Suzuri-bako” (ink stone box) as an example
I. “Monyo-gaki” (Drawing of pattern)
Draw a design with imagining the process and effect of “Aogai” in accordance with shape, size and type of products. Then, copy the design onto thin Mino paper.
II. “Kai-kiri” (Cutting shells)
There are following three ways to cut Aogai according to the design.
1) “Cutting” for making straight line with cutting knife
2) “Cutting through” for making circle/arc, eyebrow shape, spindle shape etc with chisel or carving knife.
3) “Needle cutting” for creating a desired shape of Aogai with free curving line using needle
III. “Okime” (Copying design)
After preparations of shell cutting, copy the design on the ink stone box which was already painted with lacquer (mainly either black or vermillion) called “Nakanuri” and polished; i.e. draw the design lines using Bengala lacquer on the back of the design made in above I . and copy onto the surface of “Nakanuri” with keshifun, powder made by gold and glue.
IV. “Aogai-tsuke” (Pasting shell pieces)
Paint “Roiro” lacquer (black colour) thinly over the copied design with a brush. When lacquer begins to dry, paste shell piece one by one onto the design on the surface. Normally a special stick is used to pick up shell piece. Large piece of shell is to be put into cracked pieces, or glue is used for pasting.
V. “Kebori” (Hairlines on an engraving)
After the surface of lacquer under shells completely dried off, engrave subtle design, such as the core of flowers, feathers, person’s face, the pattern of fabric etc, with needle.
VI. “Konaka-nuri” (Intermedate coating)
After having finished to place all shells, complete the product with “Konaka-nuri” and “Uwa-nuri” (final coating). “Konaka-nuri” is to put lacquer thinly on the surface, in order to solidify lacquer around the pasted shells and to prevent pool and shrink of lacquer.
VII. “Kaimuki”, “Konaka-togi” (Scraping and polishing)
When the lacquer on the surface of the placed shells dried off well, scrape off “Konaka-nuri” with chisel or carving knife. Furthermore, polish the whole surface with Shizuoka coal (Suruga charcoal block) and put final coating with fine “Roiro” lacquer efficiently filtered through “Yoshino” paper.
VIII. “Uwanuri-togi”(Polshing final coating)
Polish the whole surface smoothly with Shizuoka coal, and apply the final polishing with ”Roiro”coal (made from Japanese snowbell).
IX. “Dozuri”(Polishing)
Polish to make the surface fine, with powders of oil polish (made by kneading polishing powder and seed oil) putting on a cotton cloth.
X. “Suri Urushi”(Rubbing lacquer onto the surface)
Rub Japanese crude lacquer of the top quality onto the whole surface. After the lacquer was absorbed fully and evenly, wipe out the excess lacquer with cotton and crumpled paper, and dry off the surface.
XI. “Suri-migaki”(Polishing)
After the surface was dried off, polish the surface with seed oil and titanium white by kneading with fingers and palms.
This increases unique gloss and depth of Japanese lacquer.
The process of “Suri urushi” and “Suri migaki” is usually repeated 3 times.
XII. Completion